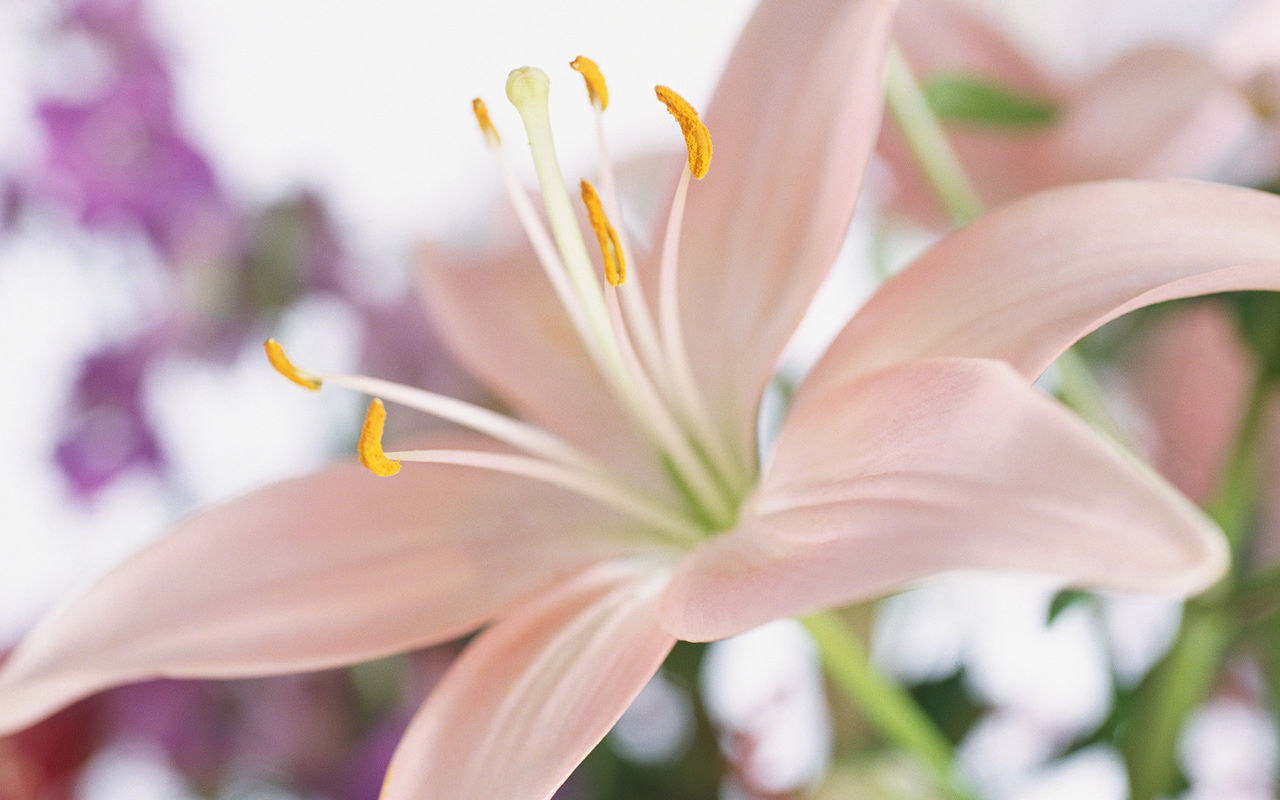

HomeMade Soap & Body Products
natural skin care
by Busybeefairies
Hot-processed homemade soaps are created by encouraging the saponification reaction by adding heat to speed up the reaction. Unlike cold-processed soap, in hot-process soaping, the oils are completely saponified by the end of the handling period, whereas with cold-pour soap, the bulk of the saponification happens after the oils and lye solution emulsification is poured into moulds.
In the hot process, the hydroxide and the fat are heated and mixed together at 80–100°C, a little below boiling point, until saponification is complete, which, before modern scientific equipment, the soapmaker determined by taste (the sharp, distinctive taste of the hydroxide disappears after it is saponified) or by eye; the experienced eye can tell when gel stage and full saponification has occurred. Beginners can find this information through research and classes. Tasting soap for readiness is not recommended, as sodium and potassium hydroxides, when not saponified, are highly caustic.
An advantage of the fully boiled hot process in soapmaking is the exact amount of hydroxide required need not be known with great accuracy. They originated when the purity of the alkali hydroxides were unreliable, as these processes can use even naturally found alkalis, such as wood ashes and potash deposits. In the fully boiled process, the mix is actually boiled (100 °C+), and, after saponification has occurred, the "neat soap" isprecipitated from the solution by adding common salt, and the excess liquid is drained off. This excess liquid carries away with it much of the impurities and color compounds in the fat, to leave a purer, whiter soap, and with practically all the glycerine removed. The hot, soft soap is then pumped into a mould. The spent hydroxide solution is processed for recovery of glycerine.

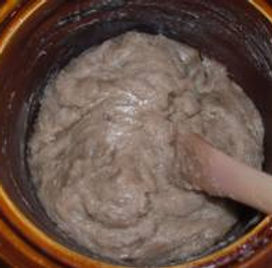